Activity-based costing is an accounting methodology that identifies activities and assigns a cost to each one based on resources consumed. It’s often associated with manufacturing but can be applied to construction as well.
Many contractors are pleasantly surprised by the results of activity-based costing in comparison with more traditional job-costing methods, which typically rely on extrapolating historical data. Whereas these methods are like using a buck knife to cut paper, activity-based costing provides a more surgically precise approach.
Cost drivers
The crux of activity-based costing is the use of “cost drivers” to estimate, track and manage project costs. A typical cost driver in construction is labor hours. When workers are on-site, the cost clock is ticking.
Pinpointing these costs with absolute precision helps the estimator price the job to allow for a reasonable profit. From there, knowing the hourly labor rate of each worker as a cost driver provides leadership with the decision-making tool they need to know when to add laborers to the job, demobilize and send workers to another project, or even send some people home.
Pinpointing costs with absolute precision helps the estimator price the job to allow for a reasonable profit.
To be clear, labor hours are just one cost driver among many. For example, an activity-based costing estimate for hanging drywall might be figured with “number of sheets” as the cost driver. Number of sheets can be broken down to “number of laborers required to hang each sheet,” “laborers’ salaries per sheet,” and “number of drywall screws required for each sheet.” This way, an overall cost per sheet of drywall can be acquired.
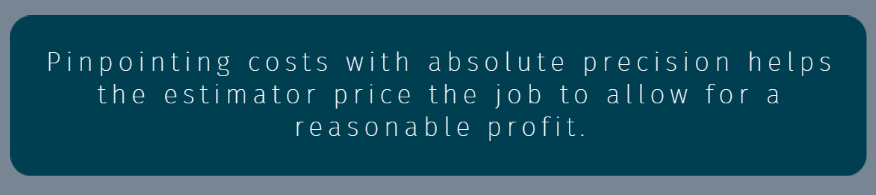
Various activities
Instead of assigning a standard square footage rate for, say, tile installation or stucco application, activity-based costing assigns cost rates to the various construction activities that go into the work. Each trade might have several different activities.
For instance, you might start with:
- Setting up the jobsite,
- Performing the work,
- Cleanup, and
- Demobilizing.
To better visualize these activities and their associated costs, you can create a grid. Identify the number of workers for each activity — let’s say a foreperson and two laborers — and the number of labor hours required. You can break down each activity in this manner, using labor hours or other cost drivers.
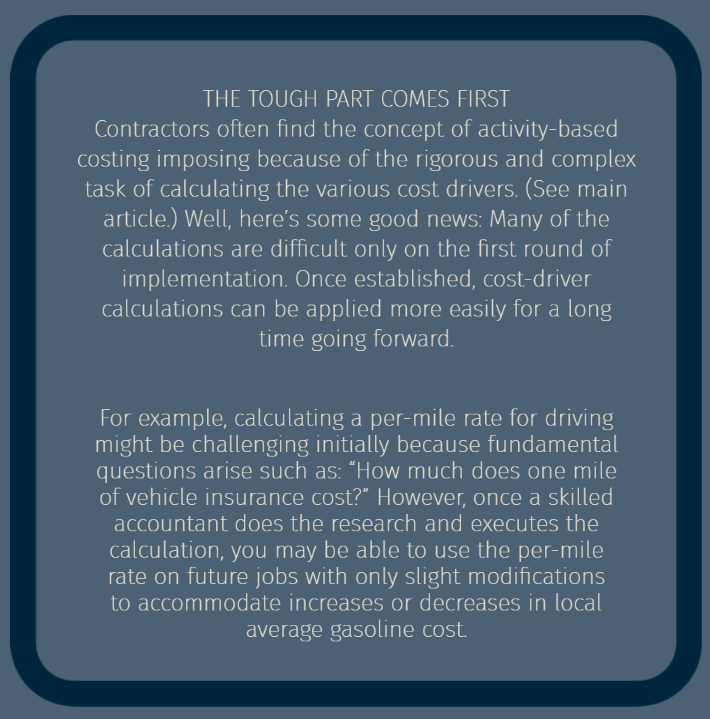
Critical calculations
As you might imagine, accurately calculating the rate for each cost driver is critical. So, before using activity-based costing, you’ll need to establish the true costs of the drivers you use.
For example, a laborer’s time might cost $20 an hour in base pay, plus 7.65% in employment taxes and an hour’s worth of health insurance and workers’ compensation coverage. Make a chart of the hourly rates for each class of employee — including project executive, project manager, superintendent, foreperson, laborer and journeyman. Anyone who touches a job in any way should have his or her true labor rate calculated if you’re going to use labor hours as the cost driver.
The choice of cost driver varies depending on the activity. For instance, a per-mile rate would be better for materials delivery. To determine the true cost of a worker who drives a vehicle, include the average gasoline cost, insurance costs and even the depreciation cost of the vehicle per mile.
Then measure the jobs by their distance to and from the location where the materials are stored or bought. Truck capacity is then calculated to see how many trips will be required so that the number of miles can be accurately estimated. Then, the per mile rate — with “distance in miles” as the cost driver — can be assigned to the activity of materials delivery on each job you price. Whereas some estimators plug in mobilization or materials delivery cost as a flat percentage, activity-based costing more accurately estimates the delivery costs by assigning “per mile” as the cost driver in this manner.
Going back to the drywall example, the cost of screws and the lineal feet of tape required to install one sheet of drywall are built into the per-sheet cost driver calculation. Once a per-sheet cost is figured, it’s then added to:
- The salary cost of the two laborers,
- A portion of the salary of one foreperson,
- An applicable health insurance and workers’ compensation cost proration, and
- A cost proration for liability insurance and other applicable costs.
This way a per-sheet drywall installation cost is calculated with hanging drywall as the activity.
The next level
Performed properly, activity-based costing enables you to more accurately estimate and track costs of construction activities on your projects. In turn, you can eliminate wasteful spending and more effectively build in profits.
But make no mistake: Activity-based costing does require a greater attention to detail, more administrative “legwork” and, above all, highly skilled accounting. If you believe your construction company is ready to take its job costing to the next level, activity-based costing might be for you.
We welcome the opportunity to put our construction industry expertise to work for you. To learn more about how our firm can help advance your success, please contact Dave Wolfenden at (302) 254-8240.